1990 - Volume #14, Issue #5, Page #10
[ Sample Stories From This Issue | List of All Stories In This Issue | Print this story
| Read this issue]
Bucket And Blade Tractor
![]() |
The 5-ft. wide, 1-ft. high blade is con¡nected to the loader arms by a pair of rods bolted to a 3-in. angle iron frame under the arms. A "push frame" is mounted between the center of the blade and the front axle. The blade pivots on a 5/8-in. dia. kingpin mounted just behind the front wheels. A 2 1/2 by 12-in. hydraulic cylin¡der is used to raise the bucket and a 2 by 8-in. cylinder is used to tilt it forward or backward. The blade can be tilted for-ward or backward and angled by manu¡ally adjusting the position of a pin inside the push frame. The tractor, which is equipped with 15-in. car tires in front and ATV balloon tires at the rear, is only 5 1/ 2 ft. long and 4 ft. wide not including the bucket.
"I built it because I needed a small tractor for working around my yard," says Ruff. "Connecting the blade to the bucket eliminates the need for a separate set of arms to operate the blade. I use the blade mainly for moving snow and level¡ing my yard so I can leave the bucket on whenever I use the blade. The bucket extends only about 2 ft. in front of the blade. I do have to remove the blade whenever I use the bucket, but it's a matter of simply removing three bolts. The bucket raises about 3 1/2 ft. Which is high enough to load heavy objects into my pickup."
Ruff used 3-in. angle iron to build the frame. He salvaged the steering column and 1,600 cc engine, equipped with an automatic transmission, from a 1971 Toyota station wagon. A second transmission (3-speed manual) was taken from a 1941 Dodge pickup. To gear down the engine, he mounted a 2-in. dia. V-pulley on the output shaft of the automatic trans-mission and ran a belt to a 12-in. pulley mounted on the Dodge transmission which is mounted on a sliding bracket. Ruff uses a turnbuckle connected to the bracket to tighten the belt. He used the rear axle and rear end from a 1949 Ford car for the tractor's front axle. He "narrowed up" the 5 1/2-ft. wide axle to 4 ft. by cutting out sections of the rear end housing and axle and then welding what was left back together. The rear axle pivots over rough terrain by means of a 6-in. long, 1-in. dia. pipe welded to a length of 3-in. channel iron. A 3/4-in. dia. rod extends through the pipe and serves as a kingpin.
Ruff made the loader arms from 4-in. angle iron and the bucket from a 15-gal. oil barrel cut lengthwise in half. He built the blade by cutting three sections from a hot water tank and welding them together. He straightened out a truck leaf spring and welded it to the bottom of the blade to provide a cutting edge. The hinged opera-tor platform can be raised out of the way for access to the two transmissions.
Contact: FARM SHOW Followup, Edwin Ruff, 940 Ironwood Dr., Moses Lake, Wash. 98837 (ph 509 765-6722).
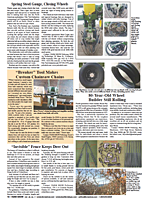
Click here to download page story appeared in.
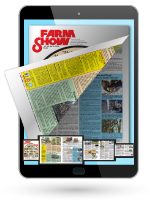
Click here to read entire issue
To read the rest of this story, download this issue below or click here to register with your account number.