You have reached your limit of 3 free stories. A story preview is shown instead.
To view more stories
(If your subscription is current,
click here to Login or Register.)
Mini Threshing Machine Ideal For Small Plots
When fields are only 10 by 45-ft. in size, a combine is too big and commercial plot threshing machines are too expensive. Orville Hillis, Charles City, Iowa, solved his small plot dilemma by building his own mini threshing machine. He raises a variety of grains and dry beans in small plots for his personal use and has
..........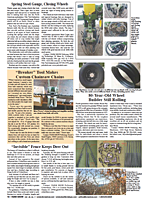
You must sign in, subscribe or renew to see the page.
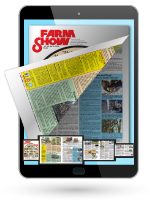
You must sign in, subscribe or renew to see the flip-book
Mini Threshing Machine Ideal For Small Plots COMBINES Miscellaneous When fields are only 10 by 45-ft in size a combine is too big and commercial plot threshing machines are too expensive Orville Hillis Charles City Iowa solved his small plot dilemma by building his own mini threshing machine He raises a variety of grains and dry beans in small plots for his personal use and has developed several lines of amaranth seed for sale I ve been raising amaranth and other small grains since 1981 and have tried different ways to thresh out the grain says Hillis I even used a bone grinder I got from a local grocery store It had different size screens that worked for the different grains but I still had to run a fan over it to clean out the chaff His home-built thresher consists of a 4 by 4-ft by 15-in wide plywood shell fitted with two cylinders a concave and a cleaning sieve The concave was made from rebar covered with pvc pipe and formed into a curve beneath the cylinders The cylinders were made from 18-in long 1-in steel shafts and lengths of auger tubing Rounds cut from 1/4-in steel to fit the auger diameter served for ends and mid shaft support Hillis fashioned rasp bars for the cylinders out of angle iron and pieces of wood The wood was cut at a taper to reduce impact on the grain kernels Grain falls through the cylinder and onto a combination straw screen/sieve Here a blower made from flat 1/4-in steel welded on a third 1-in shaft blows trash out the back The straw screen/sieve was made from an old Allis Chalmers combine sieve that was cut to fit As grain falls through the sieve air from a 12-volt squirrel cage fan rescued from an old wood-burning stove removes smaller chaff and dust The grain is collected in a pan at the bottom of the threshing chamber Power to drive the shafts comes from a pto drive A belt drives a double pulley on the first cylinder shaft which in turn drives a second pulley driving a double pulley on the main second cylinder shaft The second pulley on that shaft-drives a pulley on the main blower fan Hillis mounted the thresher on a small trailer made from an old silage cart This allows him to set up alongside his small plots I can thresh about two bushels of oats per hour with the help of a second person he says It works well on oats amaranth and sorghum and isn t too bad with soybeans With wheat and triticale you do lose some grain with the trash Hillis put his thresher together for less than $300 and plans to upgrade his design installing a straw walker above the sieve and building an adjustable concave for better threshing of problem grains Hillis is hoping to find a company to partner with to make and market his thresher He s confident there is a demand for an inexpensive small plot thresher While attending an international amaranth conference he had interest from attendees from Africa They felt his design would be ideal for small villages with lots of labor and limited capital Hillis is also marketing the amaranth varieties he has developed using selective breeding The high protein South American grain can be ground for flour or popped like popcorn Hillis likes it because it does well in years when corn doesn t His varieties yield from 1 800 to 3 500 lbs per acre depending on the weather To dry them he cuts the heads and lays them out on long racks Hillis admits the market is limited at this time He uses most of the amaranth he grows but he knows of one processing plant paying 40 to 60ó/lb depending on whether it is conventional or organic Contact: FARM SHOW Followup Orville Hillis 3020 220th St Charles City Iowa 50616 ph 641 228-4860
To read the rest of this story, download this issue below or click
here to register with your account number.