"Flipped Axle" Army Truck Converted To Front-End Loader
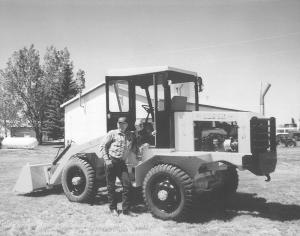 ✖  |
Flip the axles and the differential on a surplus U.S. Army deuce and a half, and you're half way to building a front-end loader. At least you are if you do it Mike Olson's way. Flipping the axles upside down wasn't all he had to do, but it made the rest pretty simple. Doing so let him reverse truck direction while retaining the original two-speed Allison transmission with its high and low manual drop box.
"I stripped the 1952 GMC truck down to the frame, axles, engine, transmission and drop box," he says. "Then I stripped the rear axle of all its springs and shackles and mounted it solid to the frame, giving me a rigid support under the loader."
A cab from a 985 New Holland combine was narrowed up 7 in. in width and mounted on the truck frame facing the former rear end. The narrower cab allowed Olson to mount loader post supports tight against the frame.
He fabricated the post supports out of 4 by 8-in. steel tubing in a U shape. They were welded to both sides and the bottom of the frame. Capped and fitted with outlets, the tubing serves double duty as the hydraulic oil reservoir for the loader. A high capacity filter system is mounted to the frame behind the uprights.
Olson fabricated his own loader arms from 3 by 6-in. steel tubing. He bought new cylinders, but recycled a bucket from a John Deere 158 loader. The pump for the loader hydraulics is belt-driven direct off the engine.
The hydraulic steering system, complete with a tilt and telescopic steering wheel, came out of a 2290 Case tractor and was mounted in the cab. Hoses connect the hydraulic orbit motor to a cylinder on the rear steering axle.
"It gives me finger tip control of the steering, nice and easy," says Olson.
Flipping the axles upside down and reversing driving direction of the truck also reversed the castor/camber of the wheels. To correct the effect, he took the knuckles off the ends of the steering axle and flipped them half a turn. This put them in just the proper position. Before reconnecting the steering axle, he moved it forward on the frame and away from the engine.
"Moving the steering axle forward provides more of a counterweight against the loader," says Olson, noting that he can still pick the rear end off the ground with a heavily loaded bucket.
He dressed up the loader tractor with new tin over the engine and painted everything a bright yellow. To protect the engine, he also fashioned a rear grill from five lengths of 1 1/2-in. diameter, oil-well chrome polish rod and 3 by 5-in. bar steel.
Originally all he wanted was a loader tractor to refill trenches made with his backhoe. His modified truck has proven to be a lot more versatile. Olson says it is great for plowing snow and moving anything he needs moved.
Contact: FARM SHOW Followup, Mike Olson, 112 St. Patrick Ave., Medicine Lake, Mont. 59247 (ph 406 789-2358).
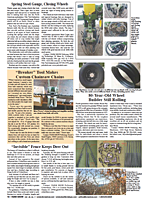
Click here to download page story appeared in.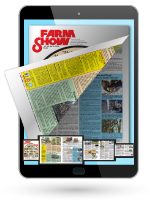
Click here to read entire issue
"Flipped Axle" Army Truck Converted To Front-End Loader TRACTORS Loaders 31-3-32 Flip the axles and the differential on a surplus U.S. Army deuce and a half, and you're half way to building a front-end loader. At least you are if you do it Mike Olson's way. Flipping the axles upside down wasn't all he had to do, but it made the rest pretty simple. Doing so let him reverse truck direction while retaining the original two-speed Allison transmission with its high and low manual drop box.
"I stripped the 1952 GMC truck down to the frame, axles, engine, transmission and drop box," he says. "Then I stripped the rear axle of all its springs and shackles and mounted it solid to the frame, giving me a rigid support under the loader."
A cab from a 985 New Holland combine was narrowed up 7 in. in width and mounted on the truck frame facing the former rear end. The narrower cab allowed Olson to mount loader post supports tight against the frame.
He fabricated the post supports out of 4 by 8-in. steel tubing in a U shape. They were welded to both sides and the bottom of the frame. Capped and fitted with outlets, the tubing serves double duty as the hydraulic oil reservoir for the loader. A high capacity filter system is mounted to the frame behind the uprights.
Olson fabricated his own loader arms from 3 by 6-in. steel tubing. He bought new cylinders, but recycled a bucket from a John Deere 158 loader. The pump for the loader hydraulics is belt-driven direct off the engine.
The hydraulic steering system, complete with a tilt and telescopic steering wheel, came out of a 2290 Case tractor and was mounted in the cab. Hoses connect the hydraulic orbit motor to a cylinder on the rear steering axle.
"It gives me finger tip control of the steering, nice and easy," says Olson.
Flipping the axles upside down and reversing driving direction of the truck also reversed the castor/camber of the wheels. To correct the effect, he took the knuckles off the ends of the steering axle and flipped them half a turn. This put them in just the proper position. Before reconnecting the steering axle, he moved it forward on the frame and away from the engine.
"Moving the steering axle forward provides more of a counterweight against the loader," says Olson, noting that he can still pick the rear end off the ground with a heavily loaded bucket.
He dressed up the loader tractor with new tin over the engine and painted everything a bright yellow. To protect the engine, he also fashioned a rear grill from five lengths of 1 1/2-in. diameter, oil-well chrome polish rod and 3 by 5-in. bar steel.
Originally all he wanted was a loader tractor to refill trenches made with his backhoe. His modified truck has proven to be a lot more versatile. Olson says it is great for plowing snow and moving anything he needs moved.
Contact: FARM SHOW Followup, Mike Olson, 112 St. Patrick Ave., Medicine Lake, Mont. 59247 (ph 406 789-2358).
To read the rest of this story, download this issue below or click
here to register with your account number.