You have reached your limit of 3 free stories. A story preview is shown instead.
To view more stories
(If your subscription is current,
click here to Login or Register.)
"Rocket Coating" Adds Extreme Wear To Metal Parts
A new "RocketCoat" process for hard-surfacing metal parts actually uses the exhaust of a tiny rocket engine to lay down tungsten carbide which is "impact fused" to the metal.
"With RocketCoat, the exhaust gasses hit the object at 10 times the speed of sound," says Jon Osborne. "We get bonding strengths that exce
..........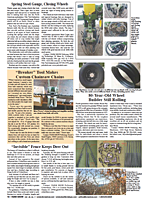
You must sign in, subscribe or renew to see the page.
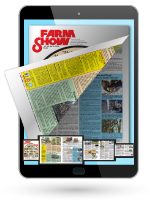
You must sign in, subscribe or renew to see the flip-book
"Rocket Coating" Adds Extreme Wear To Metal Parts SPECIALTY/SERVICES Specialty/Services 32-1-39 A new "RocketCoat" process for hard-surfacing metal parts actually uses the exhaust of a tiny rocket engine to lay down tungsten carbide which is "impact fused" to the metal.
"With RocketCoat, the exhaust gasses hit the object at 10 times the speed of sound," says Jon Osborne. "We get bonding strengths that exceed 12,000 psi and have coated surfaces as thin as 14-gauge."
Osborne's company, Extreme Industrial Coatings, has built its reputation around hard-surfacing valves, pumps, impellers, and other high-wear parts. He also repairs cast iron components, shaft bearings, and seals using several proprietary coating techniques he has developed.
In one case, a bronze impeller on a pump that recirculates wastewater at a dairy farm used to wear out every two weeks or so. After Osborne installed a RocketCoated impeller, there's no wear after 18 months.
"We've coated vacuum valves on potato seeders that normally get replaced each season, but ours aren't scratched after three seasons," he says. "Replacing them costs big bucks, along with the time to tear the machine down to its guts."
Other common uses for his expertise include pulleys and fan blades. While the pulleys are not that costly, as they wear, they tear up belts that can run as high as $1,500 on some machines. Fan blades in a variety of ag and non-ag situations quickly become pitted as blades hit dust particles. This affects the balance of the fan and its efficiency. Osborne says coatings can eliminate, or at least minimize, the wear.
Osborne, the wear control engineer and company owner, also uses plasma and flame techniques to lay down thin coatings of material on tillage wear points. He claims a quarter inch of PlasmaPlate (a 36,000¦ process that applies tungsten carbide over points subject to extreme wear) is as resistant to abrasion as 1-ft. thick steel plate.
"The plasma process melts both the tungsten carbide binder and the base metal," explains Osborne. "We've used the process on fans that were swapped out every three months and have since gone two years without replacement."
Another method, FlameSpray, uses a torch to lay down metallic and ceramic coatings, while BoroPlate welds boron carbide onto parts.
"Our niche is wear control, and we're always on the lookout for new materials as well as technologies to apply it," says Osborne. "Our electric arc spray is one that is really exciting. It gives us the technology to go in and lay down a thin skin of hard facing over large surface areas and do it economically."
He has used the process to coat the beds of large feed trucks and even corn chopper chutes.
"The chutes were a real pain in the neck, but we compared them to chrome chutes on side-by-side machines," says Osborne. "At the end of the season, ours showed hardly any wear compared to the chrome."
The material used also varies from job to job with tungsten carbide a common coating. On the chutes, Osborne used a boron carbide steel alloy called Borospray.
"It's like metallic glass with no grain structure in it and yet it approaches tungsten carbide in abrasion resistance while being lower in cost," explains Osborne.
He emphasizes that surface preparation is as important as the actual coating. He has developed several proprietary preparatory processes, including unusual media that are extremely hard and dense.
Prices vary depending on the process, material and size of the job. Osborne suggests contacting him before shipping a part, as it may be less expensive to buy a part in his area, have it coated and then ship it one way.
Contact: FARM SHOW Followup, Jon Osborne, Extreme Industrial Coatings, Airways Industrial Park, 11319 W Willow Lane, Airway Heights, Wash. 99001 (ph 509 991-1773; fax 509 299-7706; jono @extreme coatings.com; www.extremecoatings.com).
To read the rest of this story, download this issue below or click
here to register with your account number.