U.S.-Built Pellet Mills "Built To Last"
"I enjoyed reading your article about cutting edge pellet-making machines (Vol. 33, No. 1) and agree with you about the future of pellet mills. But why would you feature Chinese-made pellet mills when you can get a better built, more reliable product that's made in the U.S.," says John Elliott, sales manager at Buskirk Engineering, Bluffton, Ind.
The company recently introduced two farm-sized pellet mills. Model 800 operates either on single or 3-phase electricity and has a capacity of up to 800 lbs. of pellets per hour. Model 1200 is pto-driven and has a capacity of up to 1,700 lbs. It comes with a 3-pt. mounting frame and requires a tractor with at least 20 hp.
"These mills are priced competitively with the small Chinese-made models but perform similar to the large industrial models that cost hundreds of thousands of dollars," says John Buskirk.
According to Buskirk, both models have some features not found on other pellet mills on the market.
Low speed, high torque: The mill's main shaft spins a pair of rollers that push material through the die, rather than the die spinning like on other models. It results in higher quality, more durable pellets with fewer fines, says the company. It's also more mechanically efficient.
Multi-directional keypad: This feature is found only on model 800. At the touch of a button, the operator can vary the speed of the rollers as well as switch the rollers' direction between forward and reverse. "We call it variable frequency drive. It lets you run some materials through at a slower speed than others, to get the right amount of pressure for making the pellet. And if the rollers start to plow due to inconsistent moisture, you can reverse their direction to free them," says Buskirk.
Process wood pellets: Depending on the price, either shelled corn or commercial wood pellets can be used as a filler to reduce the cost of making pellets. "Most other mills can't handle hard commercial pellets unless you grind them up first. Our mills have enough torque to eat right through them," says Buskirk. "Some customers prefer to mix corn with pellets just because they think the addition of corn helps the pellets burn better."
Buskirk says customers who've field-tested units used many different kinds of materials, including animal bedding, horse and poultry manure, and all sorts of wood products including waste wood and sawdust.
Whatever material is used, it should contain 10 to 20 percent moisture, he says.
Depending on the kind of material, there can be a big difference in the amount of natural lignin contained. Lignin is the material that holds pellets together. Pelleting as a whole is an art rather than a science, says Buskirk. "Wood is a very fibrous product, so sometimes you need to use lubricants so the die will do a better job of pushing materials through. Common lubricants include vegetable oil, soybean oil, distiller's grain, and glycerin, or you can use commercially available binders and lubricants."
Model 800 sells for $6,499 with the multi-directional VFD and keypad. A 3-phase only version of this model is available without the keypad but with a forward and reversing switch. It sells for $5,999. Model 1200 sells for $6,999.
Contact: FARM SHOW Followup, Jon Elliott, Buskirk Engineering, 311 South State Road 301, Bluffton, Ind. 46714 (ph 260 273-0917; jelliott@buskirkeng.com; www.bus kirkeng.com).
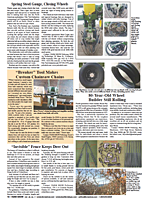
Click here to download page story appeared in.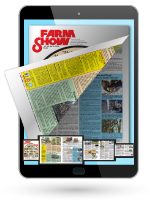
Click here to read entire issue
U.S.-Built Pellet Mills "Built To Last" ENERGY Wood Burners (65) 33-3-43 "I enjoyed reading your article about cutting edge pellet-making machines (Vol. 33, No. 1) and agree with you about the future of pellet mills. But why would you feature Chinese-made pellet mills when you can get a better built, more reliable product that's made in the U.S.," says John Elliott, sales manager at Buskirk Engineering, Bluffton, Ind.
The company recently introduced two farm-sized pellet mills. Model 800 operates either on single or 3-phase electricity and has a capacity of up to 800 lbs. of pellets per hour. Model 1200 is pto-driven and has a capacity of up to 1,700 lbs. It comes with a 3-pt. mounting frame and requires a tractor with at least 20 hp.
"These mills are priced competitively with the small Chinese-made models but perform similar to the large industrial models that cost hundreds of thousands of dollars," says John Buskirk.
According to Buskirk, both models have some features not found on other pellet mills on the market.
Low speed, high torque: The mill's main shaft spins a pair of rollers that push material through the die, rather than the die spinning like on other models. It results in higher quality, more durable pellets with fewer fines, says the company. It's also more mechanically efficient.
Multi-directional keypad: This feature is found only on model 800. At the touch of a button, the operator can vary the speed of the rollers as well as switch the rollers' direction between forward and reverse. "We call it variable frequency drive. It lets you run some materials through at a slower speed than others, to get the right amount of pressure for making the pellet. And if the rollers start to plow due to inconsistent moisture, you can reverse their direction to free them," says Buskirk.
Process wood pellets: Depending on the price, either shelled corn or commercial wood pellets can be used as a filler to reduce the cost of making pellets. "Most other mills can't handle hard commercial pellets unless you grind them up first. Our mills have enough torque to eat right through them," says Buskirk. "Some customers prefer to mix corn with pellets just because they think the addition of corn helps the pellets burn better."
Buskirk says customers who've field-tested units used many different kinds of materials, including animal bedding, horse and poultry manure, and all sorts of wood products including waste wood and sawdust.
Whatever material is used, it should contain 10 to 20 percent moisture, he says.
Depending on the kind of material, there can be a big difference in the amount of natural lignin contained. Lignin is the material that holds pellets together. Pelleting as a whole is an art rather than a science, says Buskirk. "Wood is a very fibrous product, so sometimes you need to use lubricants so the die will do a better job of pushing materials through. Common lubricants include vegetable oil, soybean oil, distiller's grain, and glycerin, or you can use commercially available binders and lubricants."
Model 800 sells for $6,499 with the multi-directional VFD and keypad. A 3-phase only version of this model is available without the keypad but with a forward and reversing switch. It sells for $5,999. Model 1200 sells for $6,999.
Contact: FARM SHOW Followup, Jon Elliott, Buskirk Engineering, 311 South State Road 301, Bluffton, Ind. 46714 (ph 260 273-0917; jelliott@buskirkeng.com; www.bus kirkeng.com).
To read the rest of this story, download this issue below or click
here to register with your account number.