2011 - Volume #35, Issue #4, Page #36
[ Sample Stories From This Issue | List of All Stories In This Issue | Print this story
| Read this issue]
They Built Their Own Shop Floor Heat System
![]() |
Bob worked with his dad, Bob Sr., to build the system. "We wanted a more efficient wood burning system so we decided to build our own," says Bob. "We installed the system when we built our shop, and it really works great. We use wood in the stove so it provides very cheap heat," says Bugger.
They welded truck wheels together, one on top of the other. The base wheel is from an old Budd semi and it supports the grate for the wood fire. On top of that wheel they welded 3 Dayton wheels. To add wood to the fire they simply lift a lid on top.
Next, they enclosed the stacked wheels with a water jacket made from a used oil tank. The heated anti-freeze mixture is then pumped through plastic tubing that runs through the shop's floor. The heat is thermostatically controlled.
A pair of homemade water manifolds mount on the wall and are connected by PEX Schedule 80 pvc tubing. Eight runs of the tubing were laid out over the shop floor before the concrete was poured. A pump circulates the water through the stove and floor.
The Buggers heat the water up to as high as 140 degrees. It's not boiling, but to be safe they installed a shut-off valve in the manifold just in case anything goes wrong and the water gets too hot.
"We spent only about half as much to build our manifold as a new one with copper tubing would have cost," says Bugger. "We don't use the system for air conditioning because cooled concrete can sweat from high humidity," he notes.
Contact: FARM SHOW Followup, Bob Bugger, Jr., 10095 N. 900 St., Effingham, Ill. 62401 (ph 217 433-3781).
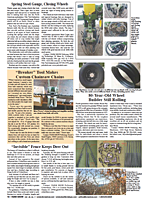
Click here to download page story appeared in.
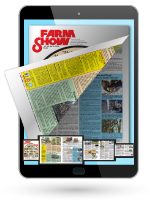
Click here to read entire issue
To read the rest of this story, download this issue below or click here to register with your account number.