2011 - Volume #35, Issue #4, Page #43
[ Sample Stories From This Issue | List of All Stories In This Issue | Print this story
| Read this issue]
Tools Turn Big Rocks Into Income
![]() |
![]() |
![]() |
![]() |
What's amazing about what Bedard is doing is that he built all of his own cutting and drilling equipment himself.
"I can dig up a big rock from a customer's yard and turn it into something beautiful," says Bedard. "Then it goes back to be used in the yard where it was found."
Rock Drill
Bedard's rock drill is a standard air drill used to drill blast holes for quarrying rock. Bedard removed the handle, turned it on its side and mounted it to a carriage. The carriage consists of an I-beam laid on its side and fitted with wheels.
"I can drill holes through 8-ft. granite posts to make one-piece light posts. If I used a regular drill I would have to drill through short pieces and stack them," explains Bedard.
The weight of the drill and carriage is sufficient to balance the bit. Minimal pressure is needed to advance the bit as it pulls itself through the rock as it drills. To keep the drill moving forward, Bedard attached a chain to the carriage and ran it forward the length of the I-beam and around a sprocket idler. From there, the chain runs back under the beam through a hydraulic-powered drive unit and back to the carriage. A spring connects the chain to the carriage.
"If the drill has slowed down a bit, the spring extends a little until the drill catches up again," says Bedard. "I made the drive from an old winch. I disassembled it and machined a piece to go over the shaft and put a sprocket on it. It's a two speed with automatic kick off. I drill at low speed and then switch to high speed to retract the bit out of the stone. When the carriage returns to home, the drive kicks into neutral."
Rock Saw
Bedard's "made-it-myself" rock saw is what really opened up "recycling" opportunities for him. It allows him to slice through 5-ton, 4 by 4 by 8-ft. rocks with ease. His only real size limit is his 17,000-lb. capacity loader.
While Bedard prefers to keep the innovative design of his rock saw under wraps, he did share some of the specifications with FARM SHOW. The diamond-coated cutting wire he uses is 45 ft. long and runs at speeds up to 73 mph. The bullwheels that carry the wire are 5 ft., 3 in. in diameter and ride on two vertical shafts used to adjust cutting height.
"On the main shaft, I have a proprietary mechanism that provides spring tension to the wire," says Bedard. "It keeps about 400 lbs. of line tension on the wire."
Aside from the wire, most other components were salvaged from other equipment. Bedard credits many friends in and out of the rock business for help acquiring needed components and providing advice.
One of those friends is Roger Belisle, a second-generation quarry man. His dad built a rock saw that was the inspiration for Bedard's.
"When I was stumped, Roger would say, æWell, you could do it this way'," says Bedard. "It seemed like having that possible solution in my back pocket would then allow me to come up with my own way to do it."
The motorized carriage the rock rides on was used in tunneling under Boston for a highway project. The rails it rides on came out of an old mine. Power for the saw is provided by a 3-phase rotary converter fed by 80-amp, 220-volt power. The 3-phase power converter is wired to a switch mechanism and then to a 7.5 hp, 1,200 rpm motor that came out of a sanding drum assembly in a woodworking shop. The electronics was one part of the project he relegated to experts.
"I had the motor taken apart, serviced and tested," says Bedard. "The same shop provided the 3-phase converter and switch, so it all matched."
Rock saws require a constant flow of water over the cut. Bedard picked up an old diaphragm pump used at construction sites. The pump is activated by a float switch to pull water out of a barrel and cycle it to the stone. The pump's 3-phase motor handles the constant on and off of the float switch.
Building the saw took Bedard 6 months of nights and weekends, filling in around his landscape work. The completed saw cost him a fraction of the $100,000 a commercial rock saw would have cost.
Bedard uses the rocksaw to make boulders into picnic tables, benches and tabletops. He also slices stone into flat pieces for doorsteps, patios and walkways. With the addition of a new motorized jig, he can even use it like a giant lathe, cutting perfect circles out of stone.
Stone Lathe
"I call the motorized jig a stone lathe," says Bedard. "It fits on the carriage of the stone saw and turns the stone as the wire is cutting it. It has a capacity of a 3-ft. radius and 3 ft. between centers and can turn a 4,000-lb. stone."
To get the control he needs, Bedard uses a 3-phase motor and a series of gear reductions. He can quickly change speeds with a sprocket change. He needs variable speeds to match the size of whatever stone he's working on.
"I can turn a slab of stone, slicing into it and cutting a round stone out of it," says Bedard. "I can also drill a hole in a slab, cut the wire, pass it through and mend it to cut a circle out of solid stone."
Bedard sees lots of uses for the round slabs he cuts, including tabletops and kick wheels for potters. Any round object now made with concrete could be done from glacial rock slabs.
Contact: FARM SHOW Followup, Paul Bedard, 173 Tibbetts Hill Rd., Goffstown, NH 03045 (ph603 497-8189).
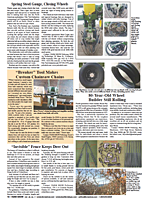
Click here to download page story appeared in.
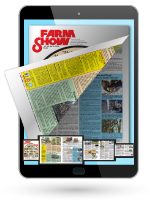
Click here to read entire issue
To read the rest of this story, download this issue below or click here to register with your account number.