You have reached your limit of 3 free stories. A story preview is shown instead.
To view more stories
(If your subscription is current,
click here to Login or Register.)
Pickup Converted To Self-Propelled Splitter
Richard Thompson spits out 4-ft. log sections for his outside furnace with his “get and split” pickup-mounted splitter. A hydraulic- powered crane pulls logs to the pickup and loads them for splitting. A sliding table even moves a half log from the first split out of the way until the other half has been split again.
..........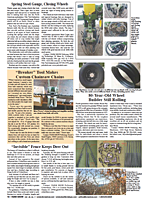
You must sign in, subscribe or renew to see the page.
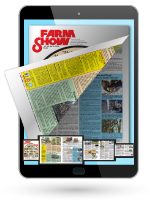
You must sign in, subscribe or renew to see the flip-book
Pickup Converted To Self-Propelled Splitter PICKUPS Miscellaneous Richard Thompson spits out 4-ft log sections for his outside furnace with his “get and split” pickup-mounted splitter A hydraulic- powered crane pulls logs to the pickup and loads them for splitting A sliding table even moves a half log from the first split out of the way until the other half has been split again “I built the splitter for a trailer but as my old Datsun pickup body rusted away I decided to convert it to a self-propelled splitter ” says Thompson What made the Datsun ideal was the open driveshaft between the transmission and transfer case Thompson pulled the driveshaft off and mounted a specially machined sprocket on it The sprocket turns a jackshaft that in turn powers two hydraulic pumps one for the rear-mounted crane and the other for the splitter “The engine has no governor on it so I can set the idle at 1 500 to 1 700 rpm’s ” says Thompson “I put the transfer case in neutral and run the transmission in fifth gear The sprocket drives the pumps at 3 500 rpm’s which provides plenty of power for both pumps ” Thompson replaced the rusted out bed with rectangular beams that serve as both a base for the splitter and as a splitting table The crane mounts opposite the splitter The 50-ft cable runs from the arm down to a hydraulic motor-powered spool centered under a vertical pipe The pipe is mounted on a 14-in sprocket connected to a second hydraulic motor with a #40 sprocket chain “The spool motor retrieves and lifts the log while the other motor turns the arm as needed toward a log and places the log on the bed for splitting ” explains Thompson “I can run one or the other but not both at the same time since they run off the same pump I have a variable control on the pump for cable speed ” To make room for the splitter Thompson cut away half the cab including part of the passenger side dash To fit the pickup he designed the splitter to pull the wedge into the log section He attached the 5-in bore cylinder to the butt plate at the rear of the splitter “I made the 12-in high wedge out of three staggered sections of leaf spring ” explains Thompson “The bottom section extends out two inches ahead of the second which is two inches ahead of the top section ” By staggering the sections of wedge the initial pressure is concentrated on a small portion of the log to be split forcing it apart As the second and third sections contact the log each of them becomes in turn the focal point for pressure “It takes less total pressure to split a log this way ” says Thompson “The spring leaves really keep an edge too I’ve only sharpened them once since I built the splitter ” Thompson says a bad back makes the pickup bed height of the splitter and splitting table especially handy To further aid in log handling he mounted a 4-ft carriage to the operator’s side of the H-beams As a log splits half falls on the carriage and the other half falls back on the table Contact: FARM SHOW Followup Thompson Farms RR 2 Box 80 Isle Minn 56342 ph 320 676-3752
To read the rest of this story, download this issue below or click
here to register with your account number.