You have reached your limit of 3 free stories. A story preview is shown instead.
To view more stories
(If your subscription is current,
click here to Login or Register.)
Self-Propelled Log Splitter
Clayton Otwell calls his self-propelled log splitter the “Split & Git”. He drives it to the field, splits the wood, and hauls it back home to stack. His Nissan 4 by 4 light truck chassis with a 318-cu. in. V-8 and a front clip from a Chrysler Fifth Avenue has plenty of power to get the job done.
“I have yet to t
..........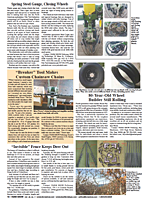
You must sign in, subscribe or renew to see the page.
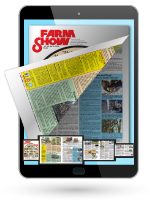
You must sign in, subscribe or renew to see the flip-book
Self-Propelled Log Splitter PICKUPS Miscellaneous Clayton Otwell calls his self-propelled log splitter the “Split & Git” He drives it to the field splits the wood and hauls it back home to stack His Nissan 4 by 4 light truck chassis with a 318-cu in V-8 and a front clip from a Chrysler Fifth Avenue has plenty of power to get the job done “I have yet to take it out of second gear ” he says “I wouldn’t want to know how fast it could go ” The Nissan had been left behind by a previous property owner when Otwell bought his property He stripped it down to the frame axles and drive train and installed the 318 engine and transmission An upright 2-in pipe welded to the front frame served as a mount for various components like the radiator and lights The front end of the frame had to be narrowed to match the Chrysler A-frame “I cut cross sections into the frame so I could ‘weasel’ the two together ” says Otwell “Then I pad-welded the sliced-up frame with steel plate to reinforce it ” While Otwell was working on the vehicle part of the project his father Jim a former boilermaker by trade was working on the splitter The younger Otwell trusted his dad do a better job on the precise welding needed “The splitter has a 4-in cylinder with a 24-in stroke ” says Otwell “The splitter wedge is a 14-in wide 1-in thick steel plate welded on edge to an I-beam The push plate is also 1-in plate ” The push plate rides on an I-beam base boxed in at the bottom with angle iron for reinforcement “This is the second one he has built and he knows how much the I-beam can twist when splitting ” says Otwell “We used all new hydraulics and powered it with a 16 gpm hydraulic pump on an 18 hp Briggs & Stratton ” Otwell had planned to run the hydraulic pump off the 318 but discovered the cost of a clutch drive was excessive for what he wanted to spend Instead he extended the frame at the front of the engine with steel pipe to hold the Briggs & Stratton At the rear and alongside the splitter Otwell installed a stacking bed “The splitting blade has wedge sides so half the chunk falls onto the bed ” says Otwell “I can catch the other half and toss it into the stack ” Otwell estimates he has around $1 000 invested in the rig and is fast getting his money’s worth out of it He has even driven it in a local parade Contact: FARM SHOW Followup Clayton Otwell 25117 Wyoming Rd Wellsville Kan 66092 ph 913 832-6231; cjmotwell@gmail com
To read the rest of this story, download this issue below or click
here to register with your account number.