2012 - Volume #36, Issue #2, Page #43
[ Sample Stories From This Issue | List of All Stories In This Issue | Print this story
| Read this issue]
1/3-Scale British Steam Engine Took 12 Years To Build
![]() |
![]() |
“If I need something, I will try to make it first,” says Stoffel. “You try to economize where you can, and cutting down a set of Boston Gears here is cheaper than importing them from England. The majority of the parts I used were pieces from a scrap pile.”
The plans, the cylinder block, piston head and crankshaft did come from England. Stoffel assembled the block and piston. He then made or fabricated most other components where he couldn›t buy them off the shelf. He did more than just cut down gears; he also made a set. A woodworker as well, he made wood patterns for the pear-shaped wheel hubs. To roll the iron plate for the wheels and other round metal parts he made a roller using a hydraulic jack to position the outside rollers.
With hundreds of rivets to make and set, he built an iron worker to punch holes and drive rivets. It uses a 5-in. cylinder with a two-stage log splitter pump.
“It’ll punch a 5/8-in. hole in a 1/2-in. steel plate,” says Stoffel. “I had to slow it down when driving rivets so they didn›t go all the way through their holes.” The iron worker and the roller were made from pictures of commercial machines he saw on the internet. He also made dies for driving the rivets.
“Trying to get the rivets to squeeze through the right way was probably the hardest thing to do,” says Stoffel.
Almost as hard to make were the wheels. After getting the hubs cast for the 2-ft. tall rear wheels, he had to roll the 6-in. wide, 1/4-in. thick flat iron to make the outer band. He also had to roll the 1/4-in. by 1-in. bands that were then welded to the inside of the outer band for securing the spokes. Everything, including the 1/4-in. by 1-in. bar stock for the treads, was riveted in place. Spokes were both riveted and bolted into place. The process had to be repeated for the downsized front wheels.
The pear-shaped hubs are designed with removable pins that connect them to the drive wheel. “British steam engines are designed with a winch that can drive off the drive wheel as well,” explains Stoffel. “You slip the pins in when moving forward or back. You pull them out when you want to use the drive wheel to drive the winch.”
Stoffel even fabricated his own boiler, only to learn boilers have to be made by a certified boilermaker. Setting his aside, he turned to Jonas Stutzman, an Amish boilermaker in Middlefield, Ohio.
“It’s a good thing I didn›t know how much it cost before I started,” says Stoffel. “The boiler for my little steam engine cost $5,500, probably half of what a full-size engine would have cost.”
U.S. regulations also required Stoffel to substitute schedule 80 steel pipe and fittings for the copper pipe and tubing used in England. He also bought commercial grade stock for anything related to water or steam pressure.
“It isn›t all perfectly to scale, but you have to accept it for what it is,” says Stoffel. “In some cases, like where the plate where the gears mount, is bolted to the sides of the boiler box, but I made it look like it’s riveted.”
In the case of the flywheel, Stoffel was able to buy a cast wheel with the right bore and radius, but he still had to bore needed holes and thread them.
“If I did it again, I would get a wider flywheel, so it wouldn›t be so easy for the belt to slip off when we use it to drive my brother’s 1922 burr mill,” he says.
One other item that Stoffel imported from England was the casting for the base of the chimney. It allows the chimney to be tilted down.
Other features of the steam engine crafted by Stoffel include the wood jacket on the boiler and the band brake on the drive. The jacket helps to insulate the coal-fired boiler.
“The wood strips are held in place by hose clamps,” says Stoffel. “Eventually I will make a steel cover for them.”
Since the engine is too small for the operator to ride on it, Stoffel made a triple duty coal wagon. The 24-in. wide, 42-in. long wagon has oak sides and a seat cushion from a Farmall A. The bottom is a stainless steel water tank that holds 18 gal. of water for recharging the boiler. Coal storage is behind the seat. The wheels are from a vintage Gehl chopper and were used to move detached heads around.
The wagon alone weighs 260 lbs. empty. The steam engine weighs 1,050 lbs. when full of water and runs on 125 to 260 lbs. steam pressure.
While only a 1/3 scale model, the engine is a working steam boiler and had to be inspected before Stoffel could fire it up for the first time. He and his brother Mike also attended a training program for boiler operators put on by the Wisconsin Historical Society.
“They went through a lot of the basics and safety like closely watching the water,” says Stoffel. “A lot of guys buy a full-size steam engine and don’t have a clue that they are sitting on a bomb.”
Making the four wheels took the longest time in the project that took nearly 12 years to complete. Stoffel still has some cables, the winch and boiler cover to add. He notes that building a second engine would take much less time now that he has the fabricating equipment and patterns in place.
So far, Stoffel estimates he has around $15,000 invested in parts and equipment. “It’s worth it for the enjoyment I get sharing it with others. I took it to a nearby event, and by the end of the day I couldn’t hardly talk.”
Contact: FARM SHOW Followup, Jim Stoffel, W2430 Century Drive, Campbellsport, Wis. 53010 (ph 920 533-5475; jimsforge@frontier.com).
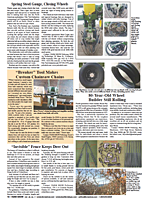
Click here to download page story appeared in.
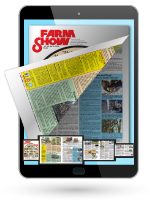
Click here to read entire issue
To read the rest of this story, download this issue below or click here to register with your account number.