You have reached your limit of 3 free stories. A story preview is shown instead.
To view more stories
(If your subscription is current,
click here to Login or Register.)
How To Tan A Deer Hide Fast
Gregory Korner, Sr., Brookville, Ind., came up with a way to tan deer hides fast, by using an inexpensive Harbor Freight concrete mixer and a 1,000 psi pressure washer. The mixer de-hairs the hide and the pressure washer removes the fat and meat.
“I seldom operate the mixer longer than 24 hrs. for any of the
..........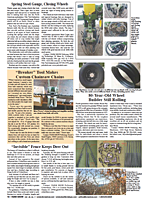
You must sign in, subscribe or renew to see the page.
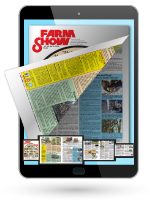
You must sign in, subscribe or renew to see the flip-book
How To Tan A Deer Hide Fast FARM HOME Miscellaneous Gregory Korner Sr Brookville Ind came up with a way to tan deer hides fast by using an inexpensive Harbor Freight concrete mixer and a 1 000 psi pressure washer The mixer de-hairs the hide and the pressure washer removes the fat and meat “I seldom operate the mixer longer than 24 hrs for any of the processes I use to tan hides ” says Korner “I came up with this system because I wanted something that would work fast I have access to a large number of deer hides from my brother’s custom slaughter house but in researching the internet I found that most people still tan hides the old way To de-hair the hide they put it in a garbage can filled with a lye solution and then stir occasionally with a stick The process takes 2 days to 3 weeks I use a concrete mixer because it provides constant agitation and works much faster ” Korner bought the 3 1/2 cu ft concrete mixer powered by a 1/3 hp electric motor at Harbor Freight for $200 He uses big hose clamps to fasten 1/16-in thick rubber roofing material over the lip of the mixer’s 18-in dia opening forming a seal that keeps the corrosive lye from splashing out Once all the hair has been removed from the hide he uses a salt solution in the mixer to flush all the lye out of the hide “It’s important to make sure the lye is completely washed out ” says Korner “When you’re done the water in the mixer should be perfectly clear It might take several washings If you don’t get all the lye out it will eventually break the hide down and ruin it ” Then he cleans the hide using water under pressure which he says is the most amazing part of the process “The old way to clean the hide requires stretching the hide over a board or sawhorse and then hours of scraping work to remove all the fat meat and membranes It’s a messy job By using a pressure washer there’s no mess and I can completely clean the hide in only about 40 min ” He lays the hide on a concrete floor and then uses a fan-shaped nozzle with the pressure washer to clean it “The nozzle works like a knife blade but since the hide is much tougher than the fat and meat and since the nozzle is fan-shaped it won’t blow a hole through the hide ” says Korner “Instead it just ‘peels’ the unwanted material right off and results in a perfectly clean hide ” He then puts the hide in the mixer again and adds a mixture of water and alum www nuts com The last step is to add a small amount of Neats foot oil and about 5 gal of golf balls in order to help soften the hide as it tumbles “How long I operate the mixer depends on how soft I want the leather – the longer it tumbles the softer it will come out ” says Korner One time he even added walnut hulls into the mixer when softening the hide “I was refurbishing an early 1900’s doctor’s carriage and wanted to replace the worn-out black leather seats I wanted the hides as black as possible so I added walnut hulls and ran the mixer for about 24 hrs It worked great ” says Korner He used three 8-ft metal furring strips to build a drying frame for the tanned hide The hide is secured to the frame with waterproof poly cords that loop through holes punched in near the hide’s edges He says his tanning process can also be used on other kinds of hides “If you just want to remove the fat and meat from the hide but not the hair you won’t need the lye ” he notes Contact: FARM SHOW Followup Gregory C Korner Sr 6020 Lookout Rd Brookville Ind 47012 ph 765 647-6314; lookoutmntrr@wildblue net
To read the rest of this story, download this issue below or click
here to register with your account number.