You have reached your limit of 3 free stories. A story preview is shown instead.
To view more stories
To view more stories
SUBSCRIBE OR RENEW NOW
(If your subscription is current, click here to Login or Register.)2025 - Volume #49, Issue #1, Page #36
[ Sample Stories From This Issue | List of All Stories In This Issue]
Custom-Built Articulated 4-WD eCub
Bill Bayer has converted various vehicles from gas to electric, but his 4-WD articulated, all-electric Cub was his most challenging yet. The project took hundreds of hours over most of a year, much of which he documented in 94 videos on his YouTube channel. It also involved developing unique articulation and steering s..........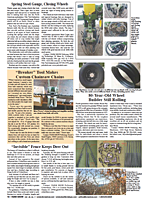
You must sign in, subscribe or renew to see the page.
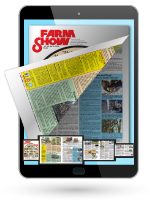
You must sign in, subscribe or renew to see the flip-book
Custom-Built Articulated 4-WD eCub ENERGY Alternative Fuels Bill Bayer has converted various vehicles from gas to electric but his 4-WD articulated all-electric Cub was his most challenging yet The project took hundreds of hours over most of a year much of which he documented in 94 videos on his YouTube channel It also involved developing unique articulation and steering systems “Hands down the articulated Cub is the best thing I’ve ever done ” Bayer proudly says “I’ve been doing electric car and tractor conversions for the past 10 years ” The articulated 4x4 has a 30-hp 80 ft /lb torque golf cart motor and a battery pack using lithium-ion modules from a Nissan Leaf car battery A DC/DC converter steps the 48-volt power down to 12 volts for the 12-volt lawn and garden battery which powers the winch lights steering motor and other 12-volt components An actuator powers a rear 3-pt hitch and high-voltage cables carry 48-volt power to front and rear e-PTO connections Bayer started his project with two Cubs headed for the scrap heap he picked up for $60 Initially he intended to turn one into a dragster and use the other for parts Things started to get complicated when he got the idea to make an articulated tractor “I started out looking at logging skidders ” says Bayer “They use a center pivot to hinge left and right with articulation handled by the front and rear axles I wanted something different “I also wanted the tractor to be all electric with no hydraulics ” he adds “Members of a forum on Facebook called Custom 4x4 Garden Tractors were a great resource ” His first step was to strip the Cubs down to their frames axles and transmissions One was a Cub 123 narrow frame with a hydrostatic transmission that he cut mid-frame setting aside the rear half and scrapping the rest including the hydraulic pump This became the rear half of the 4x4 The other Cub was an unknown wide-frame model with a three-speed that he cut off just ahead of the dash Again he retained the rear half reversing it so the transmission was to the front This time he also retained the frame of the front half and used it to extend the reversed rear The extension made room for the 48-volt battery pack charger cooling system and other electrical components Bayer tackled articulation with a pivot point extending out from a cross member under each frame A ball joint under the front extension provided left and right and the ability to flex over bumps Connecting the tops of the two frames was more challenging An advisor from the forum advised Bayer to position the upper pivot point directly over the lower one To do so he welded a triangular plate to a cross-member plate on the frame of the front unit extending the apex over the lower pivot point Bayer then made what he refers to as a floppy link similar to a tie rod linkage It connects from the triangle’s apex to a cross member on the rear frame just ahead of the wheels With articulation resolved other components began to fall into place The motor was installed over the transmission on the front frame and a mechanical connection was required to connect the two transmissions “With the input shafts facing each other I decided to make a direct drive ” says Bayer “The input shaft from the rear transmission goes to a universal joint to a spline coupler slip joint to a universal joint to a shaft to a coupler on the front transmission input shaft A cog belt runs from a pulley on the electric drive motor to an identical one on the shaft providing a 1:1 ratio while the transmissions have a 25:1 ratio ” With the drive figured out Bayer still faced the challenge of steering Like the transmission it needed to be mechanical between the front and rear halves After several false starts with an actuator he settled on using a power assist steering motor from a Nissan Versa It would power a chain drive linked to the front half frame Before fabricating a tower for the steering wheel shaft and the steering motor Bayer built the chain drive It consists of a steel plate with a 12-tooth sprocket driven by a shaft from the motor and a 42-tooth sprocket The larger sprocket has a Pitman arm welded to its top side A tie rod-type linkage fabricated by Bayer connects the sprocket Pitman arm to a bracket on the left rear side of the front half frame When the large sprocket turns clockwise the left sides of the frames move apart and the tractor steers to the right The left sides pull together when it turns counterclockwise and the tractor turns to the left The need for a chain drive was due to the eventual positioning of the seat the steering wheel support tower and other components including the upper articulation linkage Taking all the different needs into account was perhaps Bayer’s biggest challenge One example of that was designing the steering wheel support tower Bayer assembled the steering wheel with the assist motor and connected it to the chain drive He then suspended it from his shop rafters to take measurements reposition and measure again Once he was satisfied he built the tower “Packing everything together is always a challenge in a conversion You always have to think several steps ahead and consider how to make maintenance easier ” he says Packing things together wasn’t limited to the rear end and steering The space between the battery pack and the grill holds a cooling system the 600-amp contactor and a logic circuit board for the display which shows battery temperature and amps The cooling system consists of a coolant reservoir and pump with a small radiator and a waterproof cooling fan salvaged from a computer “The coolant is piped around the battery pack to a thick aluminum chill plate bolted to the inverter which is immediately behind the battery pack ” says Bayer “It keeps the sensitive electronics in the inverter from overheating ” The inverter converts the 48-volt DC power from the battery pack to three-phase AC which then goes to the induction motor The DC/DC converter and charger sit above the motor High-voltage fuses are to the side of the motor The 12-volt lawn and garden tractor battery sits between the motor and the articulation pivot point with the fuse block for the 12-volt components sitting above the battery The e-PTO connectors at the front and back of the tractor deliver power to implements and attachments including a wood chipper pressure washer tiller and multiple mowers Each has been converted to electric power or was built by Bayer to be powered by an electric motor Many of them use the same motor thanks to a rapid installation system he designed using 2-in receiver hitch components Swapping the motor from one implement to another is as easy as pulling a pin on the hitch The tractor’s rear also hosts a 2-in receiver hitch with a lip for a hitch pin and a Cat 1 3-pt hitch powered by a 12-volt electric actuator “I based the 3-pt on dimensions off a Kubota DX 2200 for the top arm pivots and lower linkage ” says Bayer “The 1 200-lb lift actuator gives the arms about 300 lbs lifting force ” The brakes for the tractor were repurposed from a 2002 DX6R and mounted on the front axle He mounted the master cylinder under the rear frame The rear axle has its original brake system “With the induction motor I really don’t need brakes ” says Bayer “When I take my foot off the accelerator the motor goes backward generating power back to the batteries while braking the tractor ” With components in place and working as planned Bayer finished the project with a customized hood made from parts of two wide-frame Cubs He had an engraved panel made to fit the original fiberglass housing It holds a voltmeter for the 12-volt battery In the middle the display for the high-voltage indicator shows the number of amp hours remaining current voltage and amps being used The rest is taken up with switches for the tractor’s various functions such as the 48-volt e-PTO lights motor etc The custom paint job was done by Kevin F a co-worker of Bayer at RJE Machinery a machine fabrication company “I really appreciate how they gave me access to the shop’s equipment whenever I needed it ” says Bayer “Kevin was able to use the paint booth there and did a great job on it ” Bayer started the project in April 2022 and drove it for the first time in February 2023 By June of that year he was wrapping it up to take it to a show in Evansville Ind when he discovered the show was nearly two weeks earlier than he thought “We went into high gear ” recalls Bayer “I picked up a new seat for the tractor the night before and when I left for the show the paint was barely dry I hadn’t even had time to put the decals on I couldn’t have done it without a lot of people from work ” Contact: FARM SHOW Followup Bill Bayer 250 Buffalo Bottom Rd Linden Tenn 37096 ph 931-589-0001; bluharo@yahoo com; YouTube: @billbayer5526
To read the rest of this story, download this issue below or click here to register with your account number.