You have reached your limit of 3 free stories. A story preview is shown instead.
To view more stories
(If your subscription is current,
click here to Login or Register.)
Modified Silo Blower Cracks Shelled Corn
You've never seen anything like the shelled corn cracker made by Kendell Hardies, Hillman, Mich., who welded 50 sickle sections into the sides of an 18-in. long, 9-in. dia. pipe and then mounted the pipe between the silo blower and blower pipe leading up into his silo.
The cutting edges of the sections extend in
..........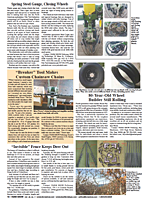
You must sign in, subscribe or renew to see the page.
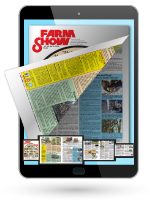
You must sign in, subscribe or renew to see the flip-book
Modified silo blower cracks shelled corn CROP STORAGE Miscellaneous 13-6-2 You've never seen anything like the shelled corn cracker made by Kendell Hardies, Hillman, Mich., who welded 50 sickle sections into the sides of an 18-in. long, 9-in. dia. pipe and then mounted the pipe between the silo blower and blower pipe leading up into his silo.
The cutting edges of the sections extend into the pipe where they crack high moisture corn as it's blown up through the pipe and into Hardies' 16 by 45 ft. concrete silo.
"It's an economical method of grinding high moisture shelled corn because it eliminates the need for a recutter blower or a roller mill," says Hardies. "The mower sections extend 1 1/2 to 2 in. inside the pipe, leaving a 5-in. dia. opening up the center of the pipe which is still wide enough that we can feed corn in as fast as the blower will take it. The mower sections crack at least 85% of the corn, and what's cracked is really cracked. However, we'd like 100% of the corn cracked so we may weld 25 or 30 more sections onto the pipe to avoid missing any corn."
Hardies originally tried cracking corn by using an International 650 forage harvester equipped with a recutter screen, but it went too slow and he didn't want to tie up his forage harvester at the silo. "I do own a roller mill, but it doesn't have enough capacity and a higher-capacity model would cost $5,000 or more. I already had a forage harvester extension pipe which just happened to be the same diameter as the silo blower pipe and it was more suitable for welding than the blower pipe because it's built from heavier gauge metal."
Hardies ground the paint off the extension pipe, then used a cutting torch to cut two rows of 2-in. long slots. He inserted a mower section into each slot, just far enough so all of the section's sharp edge extends inside the pipe. Then he used a wire feed welder to weld the sections to the pipe. The mower sections are staggered so that each section splits the difference between a pair of sections in the opposite row. To crack corn going up the center of the pipe, Hardies made two longer blades by welding the tips of- four sections together. `II hoped that the longer blades would not only crack some corn, but also divert it to the other sections for further cracking, but it doesn't seem to do that. I may try to weld a small tapered cone inside the center of the pipe, just below the sections, to divert corn to them."
Contact: FARM SHOW Followup, Ken-dell Hardies, Rt. 2, Box 179; Hwy. 451, Hillman, Mich. 49746 (ph 517 742-3045).
To read the rest of this story, download this issue below or click
here to register with your account number.